Cuối thế kỉ 20, sau một loạt các báo cáo chấn động về sai sót trong y tế ở Mỹ, người ta ráo riết đi tìm một triết lý nào đó để giảm sai sót và quản lý chất lượng trong y tế. Những ứng dụng và thành công trong ngành công nghiệp hàng không, được cho là có những đặc điểm tương đồng với y tế, đã thu hút sự chú ý của các nhà quản lý y tế. Gary Kaplan, chủ tịch Virginia Mason Medical Center (VMMC), sau cuộc nói chuyện tình cờ với một hành khách ngồi cạnh trên máy bay, hoá ra đó chính là cựu CEO của Boeing, đã bước đầu tìm hiểu về TPS như là một "cứu cánh" cho y tế: Virginia Mason Production System (VMPS).
Từ sau thế chiến 2, sự phát triển vượt bậc sau cách mạng công nghiệp, Toyota Production System (TPS) và những triết lý về quản lý của họ đã được nhiều ngành công nghiệp đón nhận như là một bí kíp. Tiếc thay, y tế, vì cho rằng y tế có những đặc điểm khác biệt, vẫn đứng ngoài cuộc chơi, cho dù những học thuyết của Frederic W. Taylor đã được chú ý đến từ đầu thế kỷ 20 với cuốn "The Principles of Scientific Management" (1911), gần hơn nữa là cuốn "Machine that changes the world" đã xuất bản từ năm 1990, và sau đó là sự phát triển vượt bậc của Toyota trở thành nhà sản xuất ô tô lớn nhất thế giới, và sự áp dụng các nguyên lý này trong mọi ngành công nghiệp, mọi mặt của xã hội. Cuối thế kỉ 20, sau một loạt các báo cáo chấn động về sai sót trong y tế ở Mỹ, người ta ráo riết đi tìm một triết lý nào đó để giảm sai sót và quản lý chất lượng trong y tế. Những ứng dụng và thành công trong ngành công nghiệp hàng không, được cho là có những đặc điểm tương đồng với y tế, đã thu hút sự chú ý của các nhà quản lý y tế. Gary Kaplan, chủ tịch Virginia Mason Medical Center (VMMC), sau cuộc nói chuyện tình cờ với một hành khách ngồi cạnh trên máy bay, hoá ra đó chính là cựu CEO của Boeing, đã bước đầu tìm hiểu về TPS như là một "cứu cánh" cho y tế: Virginia Mason Production System (VMPS). Từ năm 2002 về sau, mỗi năm đều có một phái đoàn các nhà quản lý chủ chốt của VMMC đi Nhật mà họ gọi là những chuyến hành hương, vậy cũng đủ thấy họ coi trọng triết lý đó đến cỡ nào, cái triết lý giúp họ vươn lên trở thành một biểu tượng về chất lượng, an toàn và hiệu suất...
Từ sau thế chiến 2, sự phát triển vượt bậc sau cách mạng công nghiệp, Toyota Production System (TPS) và những triết lý về quản lý của họ đã được nhiều ngành công nghiệp đón nhận như là một bí kíp. Tiếc thay, y tế, vì cho rằng y tế có những đặc điểm khác biệt, vẫn đứng ngoài cuộc chơi, cho dù những học thuyết của Frederic W. Taylor đã được chú ý đến từ đầu thế kỷ 20 với cuốn "The Principles of Scientific Management" (1911), gần hơn nữa là cuốn "Machine that changes the world" đã xuất bản từ năm 1990, và sau đó là sự phát triển vượt bậc của Toyota trở thành nhà sản xuất ô tô lớn nhất thế giới, và sự áp dụng các nguyên lý này trong mọi ngành công nghiệp, mọi mặt của xã hội. Cuối thế kỉ 20, sau một loạt các báo cáo chấn động về sai sót trong y tế ở Mỹ, người ta ráo riết đi tìm một triết lý nào đó để giảm sai sót và quản lý chất lượng trong y tế. Những ứng dụng và thành công trong ngành công nghiệp hàng không, được cho là có những đặc điểm tương đồng với y tế, đã thu hút sự chú ý của các nhà quản lý y tế. Gary Kaplan, chủ tịch Virginia Mason Medical Center (VMMC), sau cuộc nói chuyện tình cờ với một hành khách ngồi cạnh trên máy bay, hoá ra đó chính là cựu CEO của Boeing, đã bước đầu tìm hiểu về TPS như là một "cứu cánh" cho y tế: Virginia Mason Production System (VMPS). Từ năm 2002 về sau, mỗi năm đều có một phái đoàn các nhà quản lý chủ chốt của VMMC đi Nhật mà họ gọi là những chuyến hành hương, vậy cũng đủ thấy họ coi trọng triết lý đó đến cỡ nào, cái triết lý giúp họ vươn lên trở thành một biểu tượng về chất lượng, an toàn và hiệu suất...
Sự thành công của VMPS thậm chí còn thu hút đoàn 8 người từ một bệnh viện hàng đầu của Nhật (Aso Iisuka) phải bay tới Seattle, Washington để tham quan VMPS vào năm 2009.
Trong chuyến đi "hành hương", VMMC cũng mời các nhà quản lý bệnh viện khác tham gia. Năm nay, khi được mời tham gia, Bob Norton, CEO của North Shore Medical Center, đã tự hỏi: chuyến đi 7000 miles này để làm việc tại xưởng sản xuất của Hitachi có giúp ông cải thiện chất lượng của bệnh viện ở Boston của ông? Bob đã làm việc tại dây chuyền sản xuất với mục tiêu giảm waste và xác định cái gì cần cải thiện trong qui trình sản xuất. Bob và mọi người đã thực sự được mở to mắt và thấy tính khoa học của TPS áp dụng trong sản xuất công nghiệp có nguyên lý hoàn toàn có thể áp dụng vào y tế. Đó là một trong những trải nghiệm thú vị nhất của ông trong suốt 37 năm làm việc trong lĩnh vực y tế.
On the surface, it is a challenging idea: That if you work in health care in the United States you can learn a lot about improving quality and safety by traveling to Japan and working in a factory.
And yet every year for the past dozen years, Gary S. Kaplan, MD, chairman and CEO, Virginia Mason, has led a delegation of Virginia Mason team members to Japan to do just that. In recent years, people from other organizations have been invited on the trip, as well.
Here are two particularly illuminating examples from those who have made the Japan pilgrimage: one who currently works at Virginia Mason (but did not when she went on the trip), and the other who is CEO of a prestigious provider organization in Massachusetts.
Lisa Mukavitz, Administrative Director, Ambulatory Services
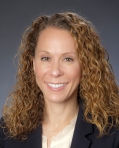
Lisa Mukavitz
“When I went to Japan – before I even started working at Virginia Mason − I really didn’t know what to expect going into the trip,” says Lisa Mukavitz, administrative director, Ambulatory Services. “I went blindly, having no idea what the trip would be like.”
She quickly discovered the essence of the trip is seeing the Toyota Production System (TPS) method and tools in action, seeing improvement and reduction of waste right before your eyes, and participating as a worker on the floor, identifying possible improvements and opportunities to reduce waste.
As a Virginia Mason outsider at the time (she was working for a different health care organization), Mukavitz was “struck by the unbelievable transparency of the Virginia Mason team,” she recalls. “There was another organization from the UK on the trip, so you had teams from two organizations outside Virginia Mason, and the transparency displayed by Virginia Mason with us outsiders in the room was incredible. To me, that really highlighted that their journey was truly focused on improvement and not on looking good.”
When the Virginia Mason team members wanted to discuss a particularly sticky problem they were experiencing in Seattle, they did not go off and huddle by themselves out of earshot of Mukavitz and others, they discussed the matter openly and sought the opinion of everyone in the room.
“They talked constantly about challenges and issues back home,” she recalls. “How can we make things better? There was a sense of raw truth. Every time we were in a conference room and had to present a component of our value stream, they were all having conversations exposing challenges and opportunities.”
Mukavitz adds, “There was no fear among the Virginia Mason group about talking truthfully about what their challenges were. They were having very candid, open debate among themselves and with us about various issues. The conversations were completely transparent. And their willingness to accept those of us from outside, encouraging us to participate in conversation − allowing outside eyes, not just as observers but as participants.’’
For years, Virginia Mason team members have come back from Japan with important insights into how to improve the lean process to serve patients. This requires, as Mukavitz puts it, “when you go on the trip you have to be open to what you don’t know and to learning what you don’t expect to learn. You have to be open to learning in a completely different way because it takes you way out of your comfort zone.”
It is an arduous journey, and while it is frequently transformative, there are some who believe a trip to the Virginia Mason Institute in Seattle to learn about lean application is just as valuable – and more convenient – than the Japan trip.
For Mukavitz, it was “an indescribable experience. I came back from Japan with a refined sense of urgency to make a difference in health care. This was about how we collectively, as an industry, accelerate improvement. That was the big picture for me when I came home.’’
Bob Norton, CEO, North Shore Medical Center
The North Shore Physicians Group near Boston had been working closely with the team from the Virginia Mason Institute to adapt the Virginia Mason Production System as the group’s management method. The effort had been quite successful.
At the time, Bob Norton, CEO, North Shore Medical Center, was closely observing the work among the physicians group. I watched the physician group’s journey in parallel to the hospital journey,” he says. “We had a much more eclectic approach at the hospital.”
But the question was whether two distinctly different improvement approaches – one for the physician’s group and another for the hospital – made sense?
“We had a good deal of debate in the hospital about whether a common methodology could help us reach our improvement goals more quickly,” says Norton. “There was not a total consensus but more people did (think it could help) than didn’t.”
Norton and his hospital leadership team engaged in discussions with Diane Miller and Henry Otero, MD, from the Virginia Mason Institute. One of the suggestions Miller and Dr. Otero made was for Norton and several colleagues to join the next delegation traveling to Japan.
The question for Norton, after nearly four decades in health care, was this: Would he travel nearly 7,000 miles to work in a Hitachi air conditioning plant to learn how to improve quality at his hospital and physician group on Boston’s North Shore?
Norton went all in. At Hitachi, he and his colleagues were part of teams that worked on the production line with the goal of reducing waste and identifying improvements in their processes.
“We were seeing the science of the Toyota Production System applied to a vastly different production line than health care, but we were seeing that the principles and concepts are exactly the same,” says Norton. “It opened everybody’s eyes. There is this myth we have been living under that our business is totally different than all other businesses, but we could see that it was just that, a myth.
“There is something about seeing it in action in the presence of a language barrier that forces you to look for universality.
“It was a life changing experience,” adds Norton. “It was one of the most interesting things I have done in my 37 years in this business. We were benefiting both from the expertise of the Virginia Mason folks but also from the expertise of lean trained leaders at a Hitachi factory as well.”
How far would you travel to change the course of history at your organization?
- All about better healthcare -
(Share nếu bạn thích, và mong bạn góp ý để chúng tôi có thể làm tốt hơn: phamngoctrungmd@gmail.com)
No comments:
Post a Comment